Efficient test solution for solid-state batteries
Background Nowadays, the competition of practical use of solid-state batteries has begun. Toyota, which is leading the way in patents, plans to open trial production EVs within 2021. Volkswagen and Quantum Scape, a Silicon Valley start-up, will start producing batteries that can significantly extend the range of PEV around 2024. Solid-state battery technology is regarded as the next-generation key technology affecting the EV industry.
A solid-state battery is a battery technology that uses solid electrodes and a solid electrolyte, instead of the liquid or polymer gel electrolytes found in lithium-ion or lithium polymer batteries. It has many advantages, such as :
* deliver higher energy densities by enabling lithium metal anodes
* avoid the use of dangerous or toxic materials
* have lower risk of catching fire
* generate only ~20-30% heat comparing with conventional batteries with liquid electrolyte under thermal runaway
* allow for faster charging, higher voltage and longer cycle life
Challenges
At present, solid-state batteries are still in the laboratory-pilot stage, and they are also facing many technical obstacles, such as the formation of lithium dendrites, low coulombic efficiency caused by interface impedance, and side reactions between solid electrolytes and positive and negative electrodes. These will lead to bad performance of fast charging and cycle life of solid-state batteries.
The basic problems of solid-state batteries used in EV mainly include charging time (current density), cycle life, safety, and operating temperature. Fortunately, solid-state batteries follow the same physical principles as traditional lithium-ion batteries. Many battery management solutions and test solutions developed for traditional lithium-ion batteries will continue to evolve and continue to be applied.
Solutions
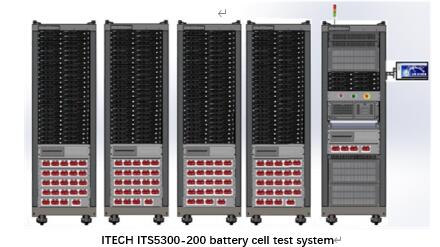
ITECH ITS5300 battery charge and discharge test system can be well applied to
1. cell cycle life test - hundreds of channels
2. road working condition simulation of EV power battery
Advantages:
a. Modular design-each channel can independently set parameters and test items
b. Strong integration-thermostat, temperature tester, internal resistance tester...
Monitoring charging capacity during the battery cycle test helps to observe the change of the battery capacity with different number of cycles. Then you can get the Coulomb efficiency, also known as the discharge efficiency (the ratio of the discharge and the charge capacity). Generally speaking, an increase in temperature helps lithium ion diffusion and at the same time reduces migration resistance, so that the first coulombic efficiency becomes higher. Electrode materials with poor reversibility will increase the amount of lithium ion inactivation, thereby reducing the coulombic efficiency.
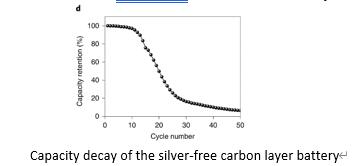
When using the battery test system to carry out long-term cycle life test of the battery, its safety and reliability are very important. Any abnormality can easily lead to the loss of test data. The overcharge and over discharge of the battery caused by unattended operation may even cause damages. The ITS5300 battery charge and discharge test system not only has basic protection functions such as OVP, OCP and OTP, but also has comprehensive alarm and protection for voltage fluctuation, current fluctuation, voltage difference protection of battery cell and so on.
The ITS5300 battery charge and discharge test system can use BMS messages as protection conditions to monitor the temperature and voltage difference changes of the cells in a battery pack in real time, very safe. Test data can be uploaded to the server in real time. With any computers within the LAN, you can remotely control the battery test system, query and access historical test data in real time, so as to quickly start battery characteristic analysis.
For battery cell testing, it can be equipped with low-power IT-M series, IT-M3600 regenerative system or IT-M3400 bidirectional DC power supply. In the size of only 1U half rack, they can achieve 800W battery charge and discharge test. For battery pack testing, it can be equipped with high-power bidirectional power supply IT6000C. A 3U unit can output 18 kW,and it can reach up to 1.152MW after parallel connection. In addition, it can also achieve seamless switching between charge and discharge. During the discharge test, up to 95% of the power can be regenerated, which helps to save cost and energy. Meanwhile, IT6000C supports arbitrary waveform generation with up to 10 million points. For complex waveform of road working conditions simulation, you only need to import the Excel file and the corresponding waveforms can be easily generated.
At present, from batteries to MW-level energy storage systems, ITECH has been able to provide solutions for various battery testing and simulation. Although it will take time to realize the industrialization of all-solid-state batteries, ITECH will surely contribute to the development of the industry by its continuous innovation on power testing technologies.
Related information
IT5300 battery charge and discharge test system
IT6000C bidirectional DC power supply
IT-M3400 bidirectional DC power supply